This page provides information on:
- The effectiveness and appropriateness of various cleaning and disinfecting strategies,
- When to clean and when to disinfect,
- How to recognize products that are hazardous to health, and
- How to assess when particular products or usages are inappropriate for schools.
In December 2020, National Education Association urged caution in over-relying on chemicals to keep students and educators safe from COVID-19. Noting that contaminated surfaces did not at the time appear to be the main way the disease spread, we argued: “over-use and misuse of toxic products, often referred to as ‘hygiene theater,’ may result in less of a focus on implementing other preventative measures, such as enhanced/improved ventilation.
It may also be making building occupants sick, especially those with asthma or other respiratory conditions.” Now, more than a year into the pandemic, we can say with even greater certainty, as the U.S. Centers for Disease Control and Prevention (CDC) has indicated, that the risk of contracting the disease from touching surfaces is “generally considered to be low.”
Despite what is now known about surface transmission of the virus that causes COVID-19, NEA remains deeply concerned about the misuse and overuse of disinfectants in schools and institutions of higher education.
NEA remains deeply concerned about the misuse and overuse of disinfectants in schools and institutions of higher education.
The Association’s concern is not based solely on the waste of time and resourses associated with over-reliance on cleaning and disinfection, Indeed, the over-use and misuse of cleaning and disinfection products can also make students and educators sick.
To be sure, there is a time and place for disinfection, particularly when, in an indoor location, there has been a suspect or confirmed case of COVID-19 within the last 24 hours. Even then, safer disinfectants should be used.
Suggested Further Reading
-
Protecting Yourself from COVID-19 (coronavirus) without Toxic Sanitizers and Disinfectants
Beyond Pesticides
-
Cleaning and Disinfecting Your Facility
CDC
-
Chemical Hazard and Alternatives Toolbox
ChemHAT
-
EPA Safer Choice Program
EPA
-
Active Ingredients for Use in Antimicrobial Products that Qualify for the DfE Logo
EPA
-
Green Cleaning, Sanitizing, and Disinfecting: A Curriculum for Early Care and Education
EPA
-
List N: Disinfectants for Coronavirus
EPA
-
Valuable resources about school
Informed Green Solutions
-
Safer Cleaning and Disinfection for Schools
Massachusetts Toxics Use Reduction Institute
-
Disinfecting Can Be Hazardous to All Students and Staff
New Jersey Education Association
-
Responsible Purchasing Network Safer Disinfectants List
OSHA
-
Explore green products & services that meet San Francisco's health & environmental requirements
San Francisco Environment Department
-
How Do You Find Safer Chemicals for the Workplace
Tools for Informed Substitution
Are you an affiliate?
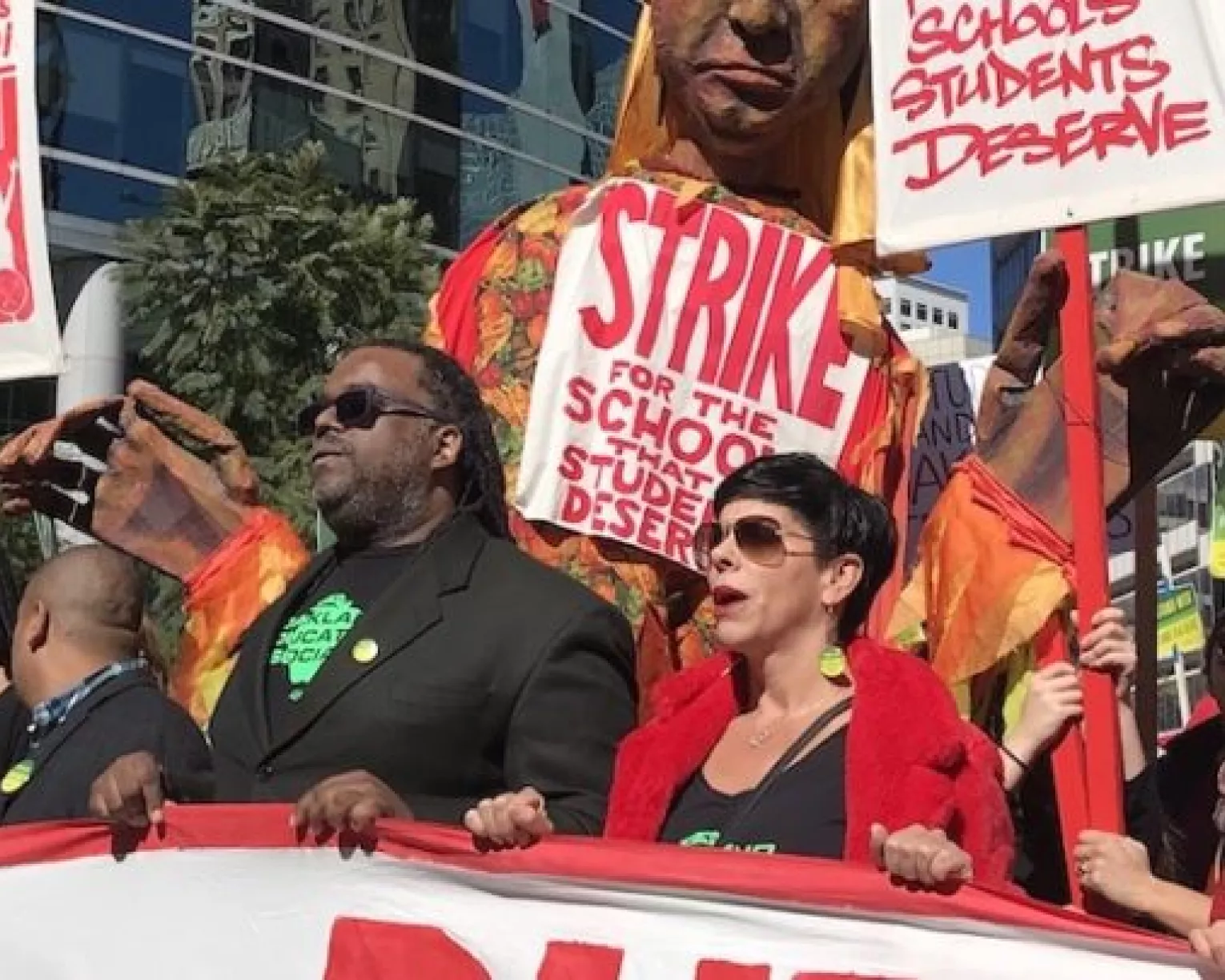